Automation
CNC working centres and special machines for manufacture tube bundle heat exchangers
In this section, Maus Italia gives a comprehensive overview of its unique CNC working centres and special machines to clearly illustrate the innovative path that a modern heat exchanger manufacturer should take to solve the basic issues of productivity, quality and safety without delay. Both the idea and the patent originated in the 1980s when Mr. Franco Agostino began to think about the concept of completely automatic operation for the Tube expansion. Subsequently, his son, Mr. Stefano Agostino, a brilliant visionary, patented the centring and automatic self-learning system for the CNC working centres. The turning point came in year 2000 with the introduction of the MA-2500, characterised by its exclusive double working axis with a consequent doubling of productivity: orbital welding had become a fully integrated and reliable system.
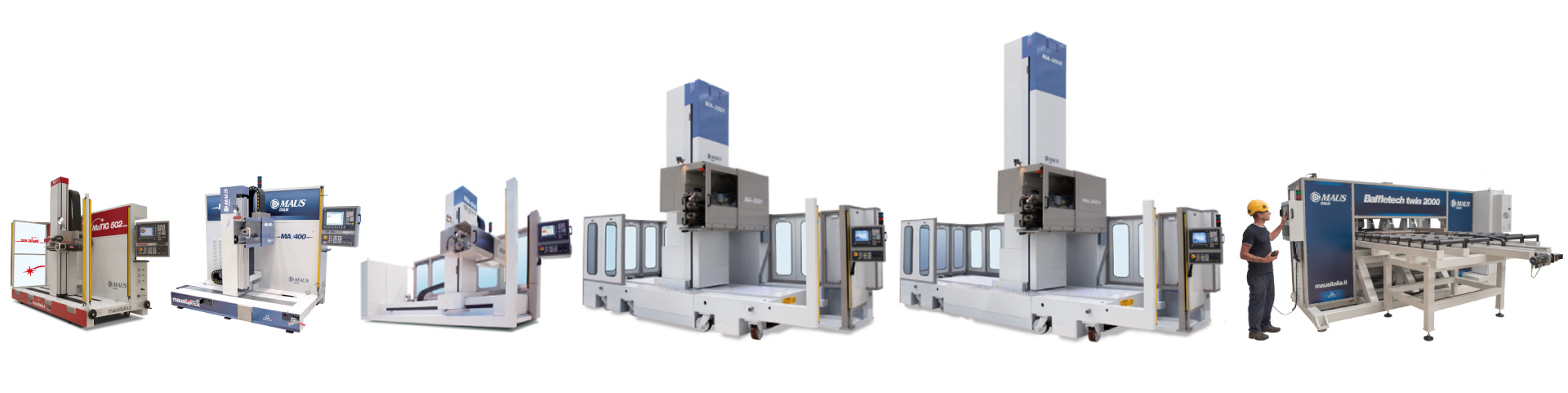
Working processes have become fully automatic
Tube expansion
Tube – tubesheet
TIG orbital welding
End facing of tubes
after insertion
Grooving
of tubesheet holes
Enter the Industry 4.0 with Maus Italia automation
The CNC/PLC machine manufactured by Maus Italia perfectly follows the requirement of the "Internet of things" being equipped of systems that allows to obtain data and statistics indispensable for handling the internal process and to be able to take strategic decision for the company development. Contact us, we will be at your complete disposal for any information.Discover the new software that can transport your company in the Industry 4.0"
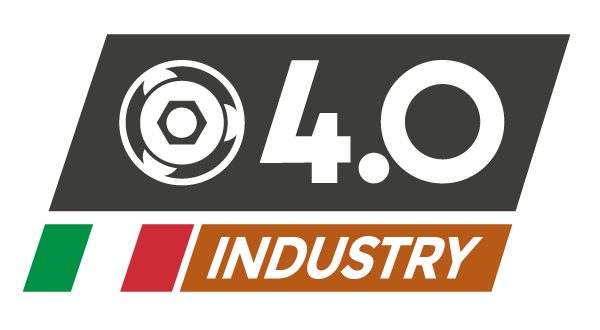
Automatic tube rolling
The automated tube rolling cycle reaches levels of productivity and quality unrivalled by traditional systems.
Total control over both torque and tube dimension allows you to highlight and configure the steps of the process during expansion, optimising work times. A further advantage of this revolutionary technology is the considerable reduction in the wear of the tools.
Complete and detailed reporting and data storing in real time.
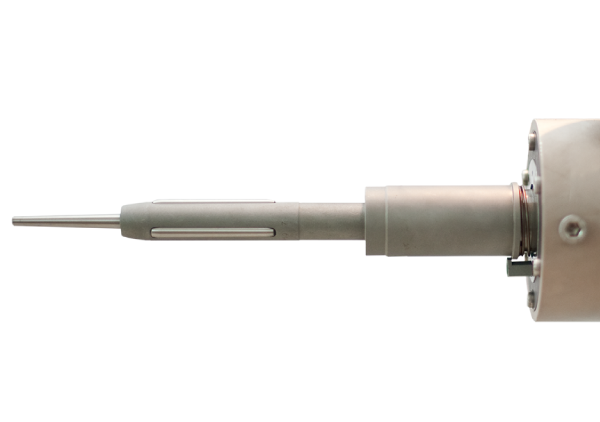
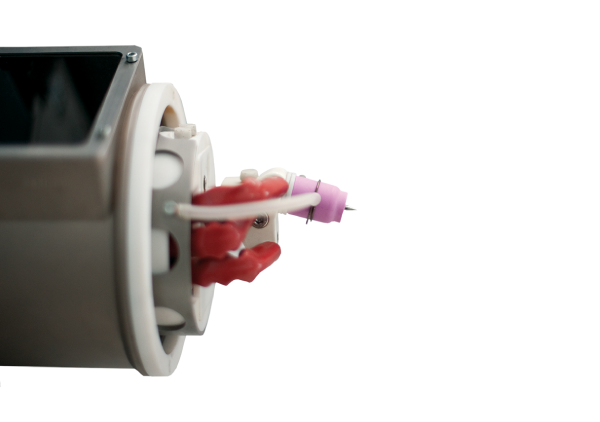
Automatic TIG orbital welding
The TIG orbital welding is the most proven and reliable technology for tube-tubesheet joints. In Maus Italia’s exclusive CNC working centre, this operation has been fully automated to ensure complete control over quality and geometry of the weld puddle.
The extremely good results make this technology unique among the range of products available on the market. Automated centring and positioning, welding fully CNC-controlled. Maus Italia has also integrated the AVC system in its CNC systems for the automated management of the electrode/piece distance, ensuring an ever more expert performance.
Automatic tube end facing
Our completely automatic system can be used for the removal of excess material as well as for welding preparation.
The automatic end-facing system compensates for deformation of the tubesheet, optimising the process in terms of both quality and production.
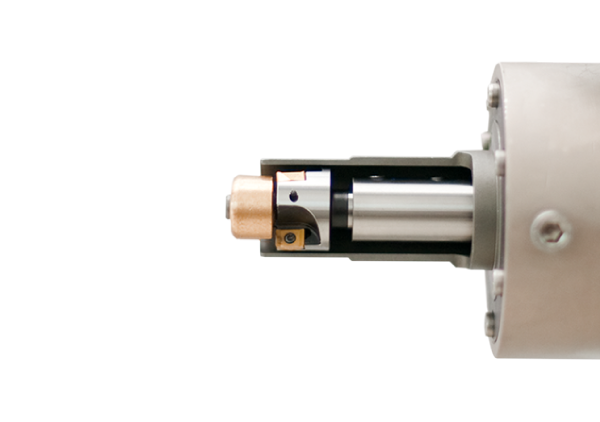
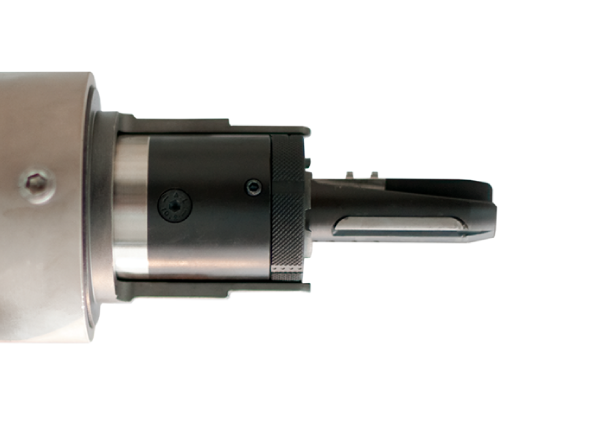
Automatic grooving
Our completely automated system can be used for making grooves inside the tubesheet holes. The automatic cycle, complete with program for management and control of the level of wear of the tool, is already programmed and only requires the inputting of speed and feed parameters.
MA Series CNC overview
Check out below all the machines designed and manufactured by Maus Italia for the automation of the processes required for the mass production of tube bundle heat exchangers.
NEWAutomatic CNC tube rolling work centre with machine vision and pallet change
MA 400
MAUS ITALIA has solved the problem of production of tube bundle batches with small dimension with an automatic tube rolling work centre complete with innovative solutions More than 600 tubes/hour - 1 cycle in less than 6 seconds